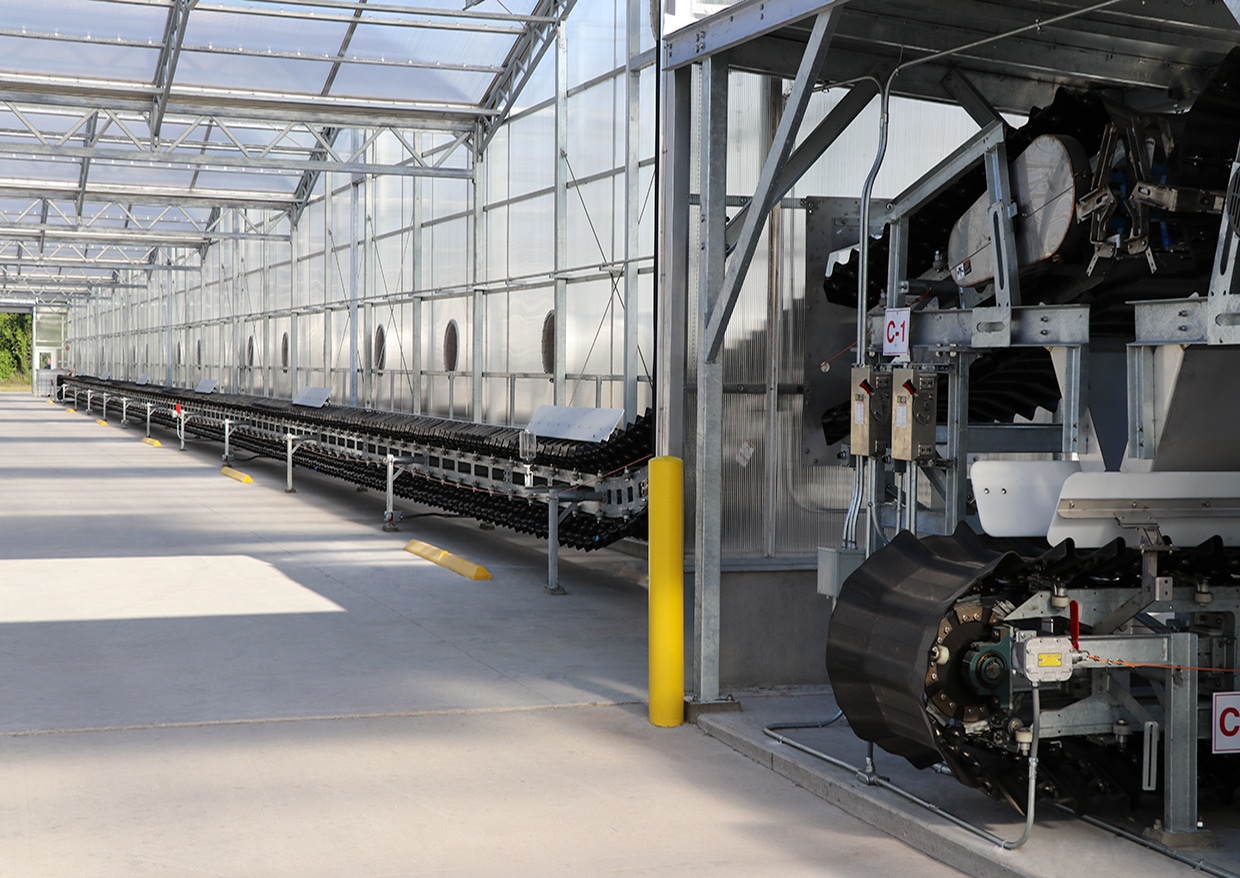
Model-H Conveyor
Mode-H – Sludge Conveyor
The Model-H sludge conveyor is the heaviest duty Serpentix designed to convey sludge up to 400 tons per hour at maximum speeds on slightly more than 100 feet per minute over distances up to 400 feet. Belt widths for Model H are 20″, 26″, and 32″.
Positive guidance and tracking for the belt are provided by roller carriages attached to and pulled through a channel track by a steel link chain. The belt is attached to and supported by the carriages and intermediate belt chain attachments. The chain is driven by a sprocket located at the drive station, and tension is set by a screw adjusted spring in the tension station.
The sludge Conveyor – Serpentix Model-H Conveyor is built to haul larger capacities of sludge over longer distances. The Serpentix Model-H implements the usage of rollers to permit longer hauls at a lower horsepower.
The Model-H like the Pathwinder, still gives clients the ability to make turns in three dimensions, and work around complex job-sites. The Model-H also uses the same belting system as the Pathwinder for easy repair and less maintenance.
Over the years Serpentix has designed and fabricated the Model-H Conveyor. This conveyor design launched the company. For thirty years each component has been scrutinized and every opportunity has been taken to improve performance.
- Convey up to 100 tons/hour
- Elevate a material up to 45° inclines
- Turn a 9-foot radius
- Conveyor lengths up to 300-feet
- Belt widths of 20″, 26″ or 32″
- Transport of materials types from solids to near-liquid
Model-H vs Flat Belt
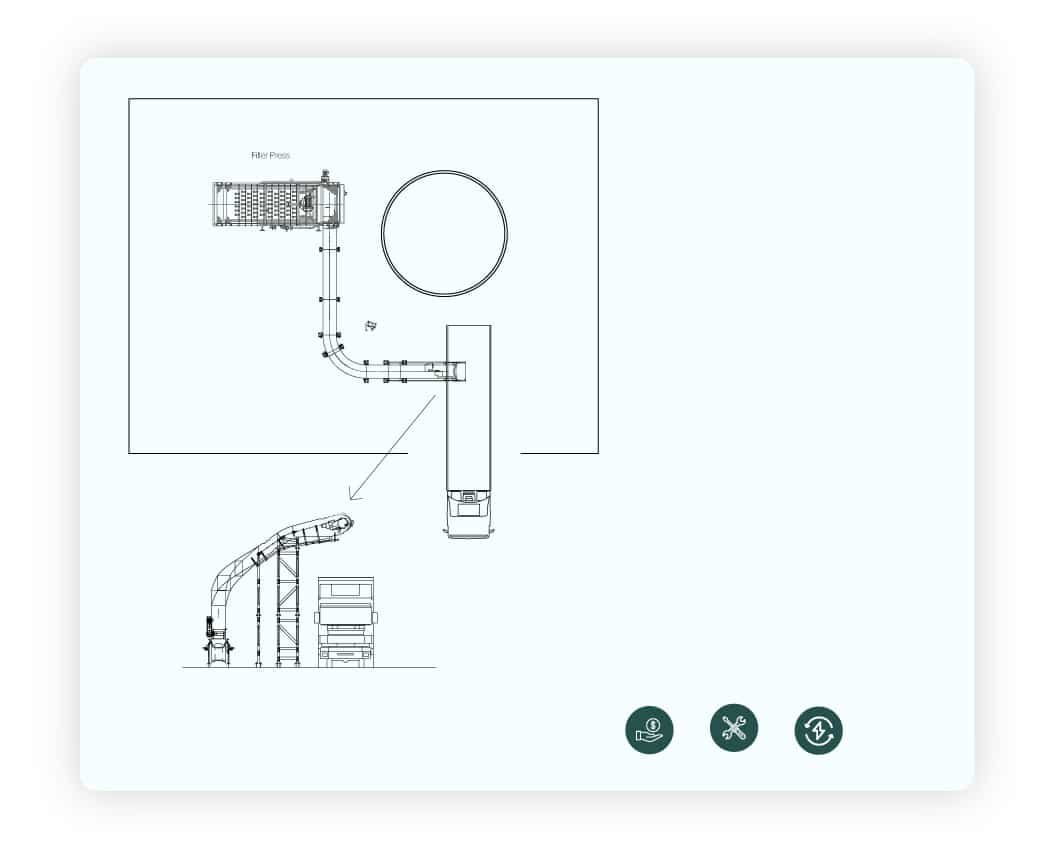
Model-H
- 45° incline angle
- 9-24 foot radius
- Energy efficiency by using one low horse power motor (2-10 hp)
- Chain driven conveyor
- Scaper system to clean dewatered sludge
- The Model-H has the ability to perform horizontal and helical turns
- Three-dimensional path
- Convey sludge, grit, screenings and bulk material in both municipal and industrial applications
- Simple and easy to use and assemble
- Belt widths of 20″, 26″ or 32″
- Low capital cost of one belt replacement
- Maintenance is primarily performed on drive and tension stations
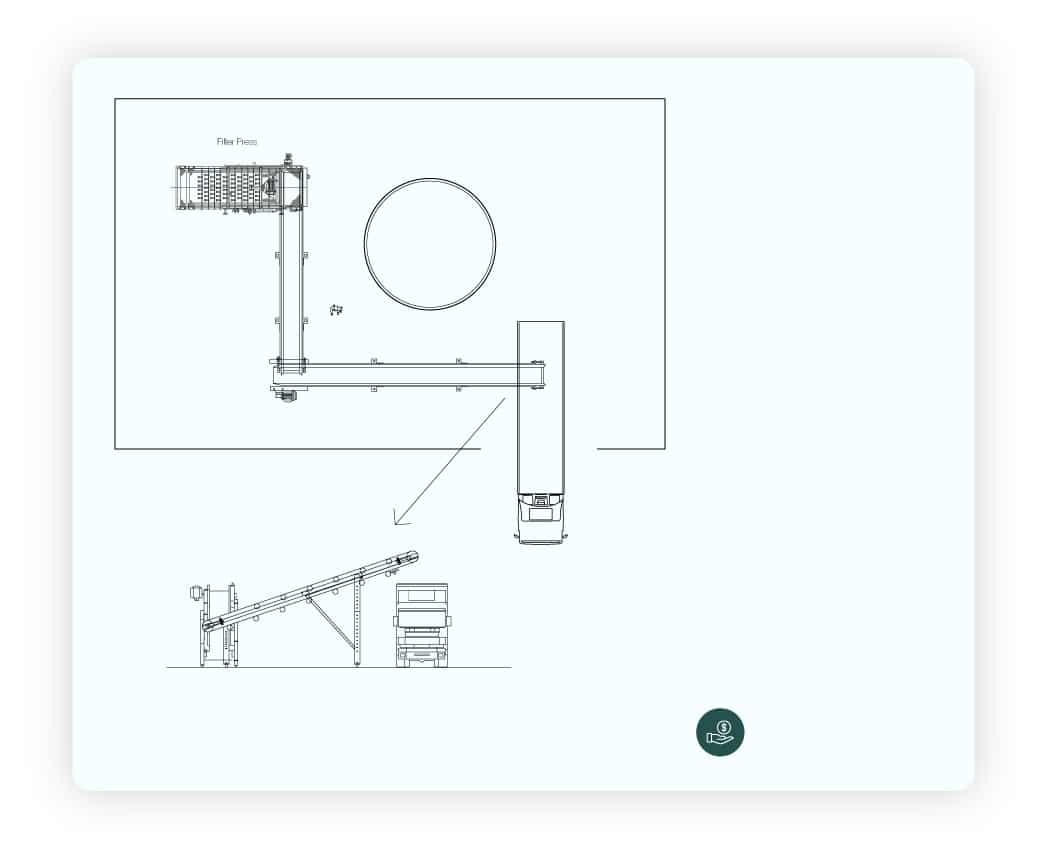
Flat Belt
- Competitive
- Increased maintenance to lubricate the idler rollers over the length of the conveyors
- Routing restrictions and poor containment
- Need of two or more conveyors to convey an offset path
- Energy-consuming (more than one motor)
- Straight line and slight inclines (max: 20°) between transfer points
- High capital costs of one belt replacement
- Belt driven system requiring frequent attention and alignment